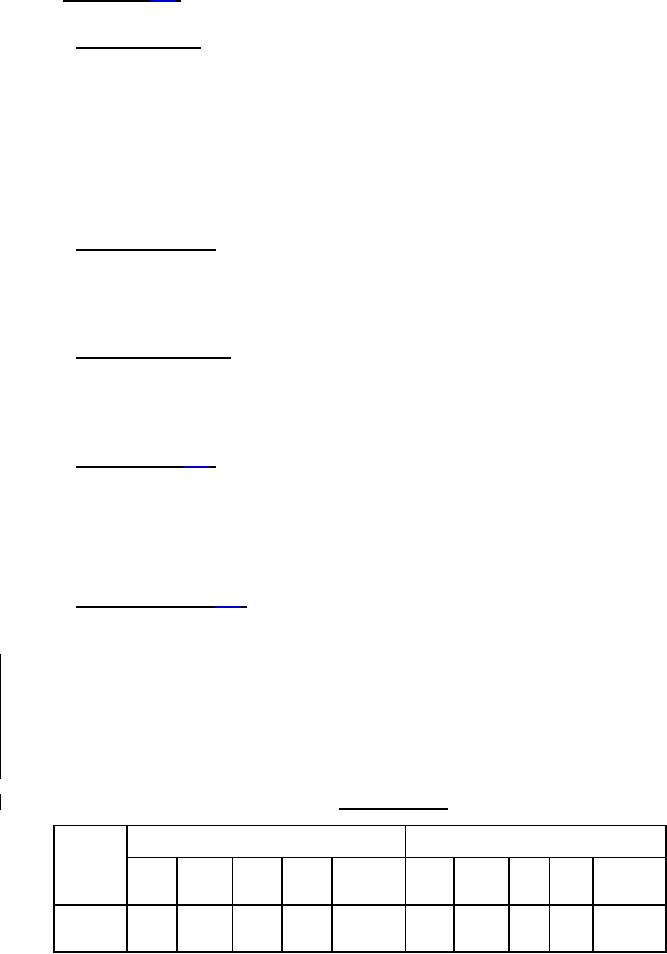
MIL-DTL-83729C
4.6.9 Vibration (see 3.13). Choppers shall be tested in accordance with 4.6.9.1, 4.6.9.2, or 4.6.9.3, as applicable
4.6.9.1 Vibration I (10-55Hz). Choppers shall be tested in accordance with method 201 of MIL-STD-202. The
following details and exceptions shall apply:
(a)
Tests and measurements prior to vibration: Dynamic contact resistance as specified in 4.6.3.1.2.
(b)
Mounting method: Rigidly mounted by normal mounting means on the vibration test apparatus.
(c)
Tests and measurements during vibration (when applicable, see 3.1 and 6.2.2): Waveform characteristics
shall be continuously monitored during vibration.
(d)
Following vibration, IR, dynamic contact resistance, starting voltage, waveform characteristics, DWV, noise
level, coil impedance and seal shall be measured as specified in 4.6.5, 4.6.3.1.2, 4.6.3.6, 4.6.3.7, 4.6.4.1,
(e)
Energize chopper coil with nominal drive during half of the vibration test time in each of the three mutually
perpendicular planes.
4.6.9.2 Vibration II (10-500 Hz). Choppers shall be tested in accordance with method 204 of MIL-STD-202. The
following details and exceptions shall apply:
(a)
Mounting method: As specified in 4.6.9.1b.
(b)
Test condition letter: A.
(c)
4.6.9.3 Vibration III (10-2,000 Hz). Choppers shall be tested in accordance with method 204 of MIL-STD-202.
The following details shall apply:
(a)
Method of mounting: As specified in 4.6.9.1b.
(b)
Test condition letter: B.
(c)
4.6.10 Acceleration (see 3.14). The choppers shall be tested in accordance with method 212 of MIL-STD-202.
The following details shall apply:
(a)
Mounting method: Rigidly mounted on the centrifuge.
(b)
Test condition letter: C.
(c)
(d)
Measurements: During the test, the waveform characteristics (with nominal drive only) shall be measured
as specified in 4.6.3.7.
4.6.11 Terminal strength (see 3.15). Unless otherwise specified herein, three terminals of each discrete design,
size, and configuration shall be tested; however, if there be less than three of such design, size, and configuration,
they shall be tested. The choppers shall be tested in accordance with method 211 of MIL-STD-202. The following
details and exceptions shall apply:
(a)
Wire leads: Bend test for wire leads shall be in accordance with test condition c. For PC board wire leads,
bend test is not applicable. Pull test for wire leads shall be in accordance with test condition A with the
applicable pull (pounds) shown in table IV.
(b)
Solder lug, pin and plug-in terminals: Choppers shall be subjected to the applicable pull force specified in
table IV in accordance with test condition A. Bend test of solder lug, pin and plug-in terminals shall be
performed by applying the applicable force (see table IV) to the outer 20 percent of terminal length and at
right angles to the terminal axis. Maintain load for 15 to 30 seconds.
TABLE IV. Pull and bend test.
Terminal
Pull pounds, test condition A
Bend test test condition C
diameter
*Test condition C (modified)
(inches)
Wire
Solder
Pin
Plug
Wire
Wire
Solder Pin Plug
Wire
leads
lug
in
Leads
leads
lug
in
Leads
PC board
PC board
<.023
2±0.2
2±0.2
2±0.2
2±0.2
2±0.2
1.0
*1.0
*1.0 *1.0
1.0
.023-.035
3±0.3
3±0.3
3±0.3
3±0.3
3±0.3
1.0
*1.0
*1.0 *1.0
1.0
.035-.047
5±0.5
5±0.5
5±0.5
5±0.5
5±0.5
2.5
*2.5
*2.5 *2.5
2.5
16
For Parts Inquires call Parts Hangar, Inc (727) 493-0744
© Copyright 2015 Integrated Publishing, Inc.
A Service Disabled Veteran Owned Small Business